Rotors
Rotors
used on these applications: |
|
chassis |
years
|
models |
3-series |
E46 |
1999-2005 |
330, 328, 325, 323 |
M3 |
E46 |
2000-2006 |
M3, M3 CSL, M3 PP |
3-series |
E36 |
1992-1999 |
328, 325, 323, 318 |
M3 |
E36 |
1994-1999 |
M3 3.0, 3.2, Evolution |
Z3 |
|
1994-2001 |
MZ3, 3.0, 2.8, 2.5, 2.3,
1.9, 1.8 |
Z4 |
|
2002+ |
3.0, 2.5 |
|
We use different types of
rotors in our brake kits, which vary by type of use.
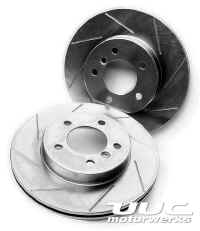 |
Standard 1-piece
rotors
[ CLICK HERE FOR MORE DETAILS ]
Excellent entry-level option suitable for
street, track/HPDE, and race use. These combine
affordable price, universal replacement sourcing, and
excellent thermal characteristics.
Black finish, slotted style only. |
|
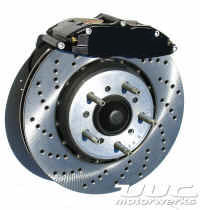 |
BMW Motorsport
floating rotors
[ CLICK HERE FOR MORE DETAILS ]
Suitable for street, track, or race use.
The "floating" design separates the central rotor
hat from the outer disk, allowing the disk to expand radially
with heat and limiting heat transfer to the hub. The
theory is that the rotor will not "cup" or distort
under extremely hot race use, resulting in better braking
performance and better rotor and pad wear. Additional
benefits include lighter weight, approximately 1.5lbs per
rotor.
Perforated (drilled) style only. |
1-piece
rotors
1-piece rotors are an excellent entry-level
option suitable for street, track/HPDE, and race use. These
combine affordable price, universal replacement sourcing, and
excellent thermal characteristics.
These rotors are rotors are slotted, black plated, and manufactured
using the best techniques and materials.
Slotting: there are many reasons to slot rotors.
Primarily, slotting aids in removal of water and debris on the rotor
surface, evacuation of hot pad "off gassing" vapor, and
provides a visual wear indicator.
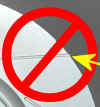 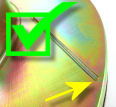 |
Details: These slots do not
extend all the way to the edge of the rotor for a very
specific reason; this maintains the structural integrity of
the rotor. Other brands with slots all the way to the
end have created "stress risers" where cracking may
develop. No such problem exists with this design.
Additionally, directional slotting enhances effectiveness. |
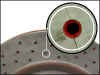 |
NO DRILLING! Drilled holes
in rotors often used for "show" are prone to
cracking and catastrophic failure. The holes create
stress risers which will lead to this sort of failure.
Additionally, drilled holes do not improve cooling,
rotary-vane rotors lose efficiency when drilled because
cooling air does not not pass through the rotor
circumferentially but is instead prematurely evacuated by the
holes.. |
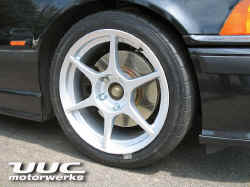 |
Plating: Multi-stage plating resists
unsightly corrosion on the rotor hub and unswept areas of
the rotor face. |
Precision: due to the ultra-precise
tolerances used for run-out, parallelism, and surface flatness,
absolutely no pre-installation machining is required for smooth
operation without vibration or shimmy.
Manufacturing details:
- Meets SAE standards for brake rotor iron.
- Alloying: Copper and Chromium added to achieve
specific hardness and tensile strength.
- Precision-controlled cooling during the casting
process creates a uniform distribution of graphite flakes, thus
increasing wear resistance and the ability to dissipate heat. In
contrast, premature cooling of cast iron can cause iron brittleness,
thus making the brake rotor more likely to warp or crack, especially
when overheated under hard braking conditions.
- Run-out less than .004".
- Parallelism of machined surfaces within
.0005" tolerance.
Floating
rotors
Genuine BMW Motorsport floating rotors as used on the European-spec
versions of the M3 and M3 CSL.
Suitable for street, track, or race use. The
"floating" design separates the central rotor hat from the
outer disk, allowing the disk to expand radially with heat and
limiting heat transfer to the hub. The theory is that the
rotor will not "cup" or distort under extremely hot race
use, resulting in better braking performance and better rotor and
pad wear. Additional benefits include lighter weight,
approximately 1.5lbs per rotor.
BMW Motorsport uses a "radial floating" design where the
floating connectors between the rotor hat and the rotor disk connect
in the center of the disk between the inside and outside face planes
using a radial (straight out) pin. It's a very interesting
construction that is not simply "assembled" but built all
together at the foundry level.
click pics for a larger
view: |
close-up: |
exploded view: |
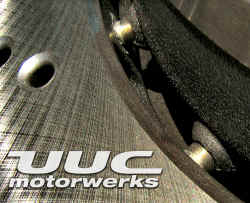 |
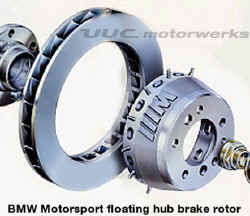 |
What's even better is that the Motorsport floating rotors are a
"complete replacement" design - you get a new hat every
time you replace the rotor, at a much lower cost from BMW Motorsport
than the "disk only" cost of aftermarket rotors with other
BBKs. When you start comparing costs, especially for race use, this
really adds up. For an interesting ongoing-costs comparison, see
this page: [ CLICK HERE ]
|